Alan R.
11-08-2022
XTRUSION OVERLAND XTR1
The makings of a truly customizable bed rack

Truly Modular, Truly Yours.
Xtrusion Overland was born out of a passion for the outdoors and a necessity to create in my own language a cargo solution for all my diverse adventures. While there were some great bed racks in the market, they all dictated in one way or another how I was to pack, and in my nature to tinker and modify things, none of those were really a good platform to get started on. I have a background in Design Engineering although, most of my professional career was in Aerospace Manufacturing. So what could I do about it?
Covid-19 was in full force, work was slow so I decided to create a truly modular rack concept. One that I could decide on which characteristics like height or length fit my needs most, but also that it could be a platform that could adapt with time as my needs changed. If I ended up trading in my truck, I could order a couple pieces and I can use it on a new truck, or if I needed a different height, I could once again get a few components and get back on the road. Nothing else in the market allowed for this!
Meet XTR1 - Prototype 1

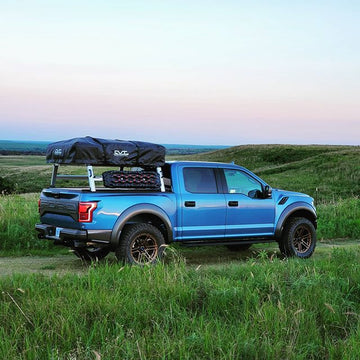

The Extrusion Profile that started it all.
The T-Slot aluminum profile I chose was one that I had worked with in the past in industrial settings. Some of you might be familiar with it under the brand name of 80/20 although, that became more of a known term for the profile rather than just a brand. Like the "Kleenex" of the T-Slot profiles. There are several brands that produce this profile in specific standards. There are metric versions like the 10 series (10mm x 10mm), 20 series (20mm x 20mm), 30 series, 40 series and 45 series. There are also US Standard versions like the 10 series (1" x 1"), or the 15 series (1.5" x 1.5"). I decided to use the US Standard version as my focus was to have a US Made product.


However, the most important factor was the standardization and compatibility of hardware. There was no point in re-inventing the wheel by using a different standard here. This really allowed me to get creative in building structures and sub-structures without the high development costs. And of course it would allow the end user to tinker with the system with readily available components!
But, none of the standard components had been created with dynamic forces in mind. (When the thing is mounted on a vehicle, exposed to lateral forces and a lot of acceleration and deceleration). That's when my background in Design and CNC machining became handy. I created a corner bracket that would join the crossbars to the uprights in the strongest and most efficient way. Now I only had to figure out a way to mount it on the bed rail. At this point, all of the structural components have been done in high grade aluminum with strength similar of steel. However, in thinking of a mounting bracket for the bed rail, it made sense to do it in sheet metal form and from a manufacturing perspective the simple route was to go back to steel. Stronger than the equivalent sheet metal aluminum and less prone to fatigue and cracks. This was how a new T-Slot cargo management system was born. The Erector Set of Bed Racks!


All the components were done. I could now set to create an awesome bed rack system that could be cut to size and re-arranged as pleased. However, the biggest challenge yet was on how to create a reliable process to bring this to market.
There were literally thousands of combinations as I wanted to bring options to the consumer. Creating a robust manufacturing system has been the number one challenge since day uno and something that we continue to perfect. It took many sleepless nights and lots of head scratching but at least we now have a reliable system to help us ship this to you in a cost effective way.
As of this blog post and since 2021 we have now sold thousands of bed rack kits. And as we have suffered a lot in supply chain disruptions in the post Covid era, we also have the privilege of having an awesome customer base that gets excited just as we were about the possibilities of this system to truly customize their rigs for their big adventures. We have grown from a garage part time gig to a small business. And we look forward to the next big growth to keep bringing products that will continue to help you translate your passion for off-roading and the outdoors into a true expression of your self.

The possibilities are endless!
Here is a video clip of one of our first trade shows, the MOORE EXPO in 2021, where I go over some of the features of that build. One thing you'll notice is the main slide out. We haven't yet figured out the reliable manufacturing process for this to go full scale as a product offering, but the main take away is that there are many off-shelf components that can be adapted thanks to some of the sub-structure and components we've created. As we add resources and expand, we will bring you a reliable full slide out that is easy to remove for access, is lightweight and cost effective.
The Community.
As I mentioned, one of the best privileges of Xtrusion Overland is its Community of customers and prospective customers. Join the Facebook Group to share your thoughts on your build and ask for advice from others as they on on the Xtrusion journey!

You can also follow us on Instagram @XtrusionOverland
Author

Alan R.
Co-Founder and President
Xtrusion Overland